High-Quality Silicon Carbide Products | Advanced Ceramic Solutions
PRODUCT PARAMETERS
Description
Overview of Silicon Carbide Powder
Silicon carbide (SiC) powder is a high-performance ceramic material composed of silicon and carbon. Known for its exceptional hardness, thermal stability, and wear resistance, SiC powder is widely used in abrasives, cutting tools, refractory materials, and advanced technological applications like semiconductors and electric vehicle components.
Features of Silicon Carbide Powder
Exceptional Hardness: One of the hardest known materials, second only to diamond, making it ideal for abrasive and cutting applications.
Thermal Stability: High resistance to thermal shock and can withstand extreme temperatures, enhancing its utility in refractory and high-temperature environments.
Chemical Inertness: Resistant to most chemicals, including acids and alkalis, ensuring durability in harsh conditions.
Wear Resistance: Excellent wear resistance properties make it suitable for demanding mechanical applications.
Electrical Conductivity: Depending on the purity and doping levels, SiC can exhibit varying degrees of electrical conductivity, useful in electronics.
(Sintering Of Silicon Carbide Ceramics With Additives Industrial Furnace)
Specifications of Sintering Of Silicon Carbide Ceramics With Additives Industrial Furnace
The sintering furnace for silicon carbide ceramics with additives handles high-temperature processes needed to create dense, durable ceramic components. It works in temperatures up to 2200°C. This range suits materials requiring extreme heat for proper bonding. The furnace structure uses high-purity alumina insulation. This material resists thermal stress and chemical reactions during sintering.
The furnace supports controlled atmospheres like argon or nitrogen. These gases prevent oxidation and keep chemical stability. Additives like boron carbide or aluminum oxide improve sintering. They lower energy use and boost final product strength. The furnace design allows precise control over heating rates. This avoids cracks or defects in the ceramics.
Heating elements are made of molybdenum disilicide. They provide steady heat distribution and handle repeated heating cycles. The chamber lining uses multilayer refractory materials. These layers trap heat and improve energy efficiency. Temperature sensors monitor conditions in real time. Adjustments happen automatically to keep results consistent.
The furnace includes advanced cooling systems. Gradual cooling prevents thermal shock. This maintains ceramic integrity. Loading areas are customizable. They fit different part sizes and shapes. Safety features include pressure release valves and emergency shutoffs. These protect both the product and equipment.
Power requirements vary by model. Standard units run on three-phase electricity. Larger versions may need higher voltage inputs. Energy-saving modes cut power use during standby periods. Data logging tracks each sintering cycle. Users can review trends and optimize settings.
Maintenance focuses on replacing heating elements and insulation over time. Regular checks ensure gas systems work properly. The furnace operates in industrial settings like aerospace or automotive manufacturing. It meets standards for precision and reliability. Performance tests confirm temperature accuracy and atmosphere control. Operational training covers setup, safety, and troubleshooting. Technical support helps with upgrades or part replacements.
Durability comes from robust construction and quality materials. The furnace resists wear from constant high-heat use. Custom configurations address specific production needs. Options include extra gas ports or expanded chamber sizes. Process automation reduces manual input. This increases output and lowers error risks. Energy recovery systems capture waste heat. They reuse it to preheat incoming batches. This cuts overall energy costs.
(Sintering Of Silicon Carbide Ceramics With Additives Industrial Furnace)
Applications of Sintering Of Silicon Carbide Ceramics With Additives Industrial Furnace
Sintering silicon carbide ceramics with additives improves their performance in industrial furnaces. This process combines silicon carbide powders with materials like boron, carbon, or aluminum. The mixture is heated under controlled conditions to form a dense, durable material. These ceramics withstand extreme temperatures, resist wear, and handle harsh chemicals. Industrial furnaces use them for high-temperature processes where metals or other materials fail.
Silicon carbide ceramics sintered with additives work well in furnace parts exposed to heat above 1600°C. They line kilns, furnaces, and reactors. Their thermal stability keeps furnace structures intact during prolonged heating. This reduces downtime for repairs. They also serve as heating elements or supports for materials being processed. Their high thermal conductivity spreads heat evenly, improving product quality in industries like glass manufacturing or metal heat treatment.
The chemical resistance of these ceramics matters in corrosive furnace environments. They handle reactive gases, molten metals, and acidic fumes without degrading. This makes them ideal for semiconductor production or chemical processing furnaces. Additives enhance their mechanical strength, letting them bear heavy loads without cracking under stress.
Energy efficiency is another benefit. Silicon carbide’s low thermal expansion reduces energy waste. Furnaces using these ceramics heat up faster and maintain temperatures with less power. This cuts operational costs in industries like steelmaking or ceramics production.
Aerospace and automotive sectors use sintered silicon carbide components in furnace systems for manufacturing high-performance parts. Their ability to handle rapid temperature changes suits applications like turbine blade sintering or brake system production.
Durability and cost-effectiveness drive their adoption. While initial costs are higher than traditional materials, their longer lifespan and lower maintenance offset expenses. Industries relying on precision and reliability increasingly choose silicon carbide ceramics for furnace upgrades.
Company Introduction
Welcome to It-Chuiko, a premier international supplier of high-quality silicon carbide powder and silicon carbide ceramics. Our products are renowned for their exceptional hardness, thermal stability, and wear resistance, making them ideal for abrasives, cutting tools, refractory materials, and advanced semiconductor applications. We serve a diverse range of industries, including automotive, aerospace, and electronics, with a commitment to quality and innovation. With state-of-the-art production facilities and rigorous quality control, we ensure that our customers receive superior products tailored to their specific needs. Partner with us for reliable, high-performance materials that drive your business forward.
If you have any questions, please feel free to contact us(nanotrun@yahoo.com).
Payment Methods
T/T, Western Union, Paypal, Credit Card etc.
Shipment Methods
By air, by sea, by express, as customers request.
5 FAQs of Sintering Of Silicon Carbide Ceramics With Additives Industrial Furnace
Sintering silicon carbide ceramics with additives in industrial furnaces involves specific steps. Here are common questions. What do additives do during sintering? Additives help silicon carbide particles bond better. They reduce the high temperatures normally needed. This makes the final product denser. Additives also improve mechanical properties like strength. Which additives work best for this process? Common choices include aluminum oxide, boron carbide, or carbon. Aluminum oxide speeds up densification. Boron carbide lowers sintering temperatures. Carbon removes surface oxides from silicon carbide particles. Each additive serves a different role based on the desired outcome. What temperature range is ideal? Most sintering happens between 1800°C and 2200°C. The exact temperature depends on the additive type. Furnace conditions like pressure and atmosphere also matter. Using the right temperature prevents defects. It ensures the ceramic reaches full density. What challenges come with this method? Uneven heat distribution can cause weak spots. Additives might not mix uniformly with the powder. This leads to inconsistent material properties. Controlling the furnace atmosphere is critical. Oxygen or moisture can react with additives. This affects the ceramic’s quality. Proper furnace calibration solves many issues. How do safety protocols differ here? High temperatures demand heat-resistant furnace linings. Operators need protective gear against extreme heat. Additives like boron carbide require careful handling. They can produce harmful dust. Proper ventilation systems are essential. Regular equipment checks prevent accidents. Follow manufacturer guidelines for additive storage. This minimizes risks during production.
(Sintering Of Silicon Carbide Ceramics With Additives Industrial Furnace)
REQUEST A QUOTE
RELATED PRODUCTS
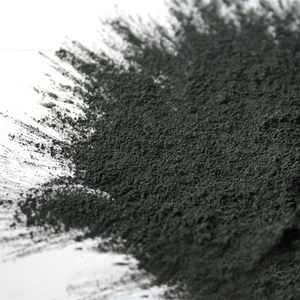
Grinding Non-Ferrous Materials Pure Black Silicon Carbide Sic 88 Powder
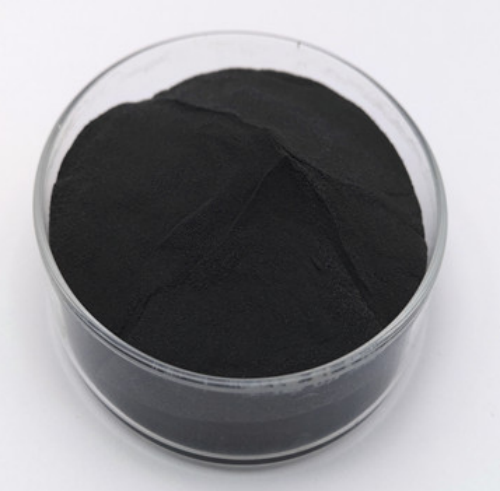
Factory Supply Black Silicon Carbide Powder Particle Size Green Silicon Carbide For Furnace
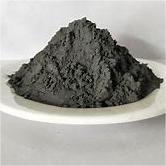
composite metal powders silicon carbide sealing ceramic sintering Powder metallurgy sintering furnace

OEM 98% Purity Green Black silicon carbide Abrasives powder Carborundum Grain
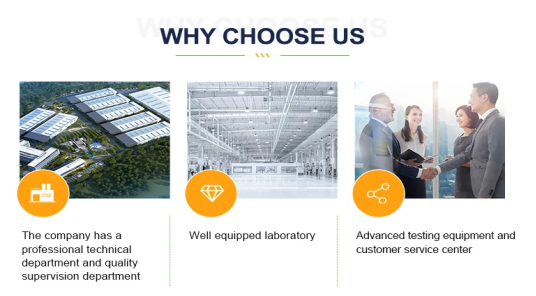
Best Black Silicon Carbide powder 24 Mesh 36 Mesh 60 Mesh Carborundum Grit
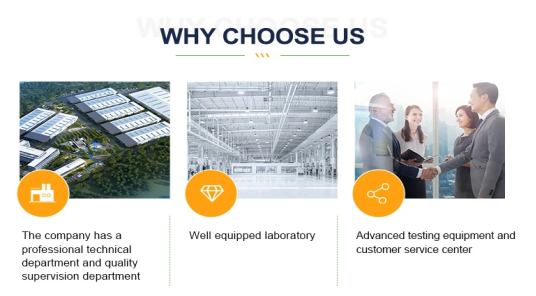