High-Quality Silicon Carbide Products | Advanced Ceramic Solutions
PRODUCT PARAMETERS
Description
Overview of Silicon Carbide Powder
Silicon carbide (SiC) powder is a high-performance ceramic material composed of silicon and carbon. Known for its exceptional hardness, thermal stability, and wear resistance, SiC powder is widely used in abrasives, cutting tools, refractory materials, and advanced technological applications like semiconductors and electric vehicle components.
Features of Silicon Carbide Powder
Exceptional Hardness: One of the hardest known materials, second only to diamond, making it ideal for abrasive and cutting applications.
Thermal Stability: High resistance to thermal shock and can withstand extreme temperatures, enhancing its utility in refractory and high-temperature environments.
Chemical Inertness: Resistant to most chemicals, including acids and alkalis, ensuring durability in harsh conditions.
Wear Resistance: Excellent wear resistance properties make it suitable for demanding mechanical applications.
Electrical Conductivity: Depending on the purity and doping levels, SiC can exhibit varying degrees of electrical conductivity, useful in electronics.
(composite metal powders silicon carbide sealing ceramic sintering Powder metallurgy sintering furnace)
Specifications of composite metal powders silicon carbide sealing ceramic sintering Powder metallurgy sintering furnace
The composite metal powders silicon carbide (SiC) sealing ceramic sintering powder metallurgy sintering furnace is engineered for high-performance processing of advanced materials. Designed to handle the unique requirements of sintering composite metal powders and silicon carbide-based ceramics, this furnace ensures precision, durability, and efficiency in industrial and research applications. Below are the key specifications:
Temperature Range: The furnace operates at temperatures up to 2200°C, accommodating the high sintering demands of silicon carbide ceramics and composite metal powders. Uniform heating is achieved via advanced heating elements, such as molybdenum disilicide (MoSi2) or graphite, ensuring consistent thermal distribution (±5°C across the chamber).
Atmosphere Control: Supports multiple atmospheres, including inert (argon, nitrogen), vacuum (up to 10^-3 Pa), and hydrogen environments. This flexibility prevents oxidation and enables contamination-free sintering of reactive metals and ceramics.
Heating Rate & Cooling: Adjustable heating rates up to 20°C/min, with programmable cooling systems (natural, forced gas, or water-cooled) to optimize material microstructure and mechanical properties.
Chamber Dimensions: Customizable chamber sizes (standard models range from 100x100x100 mm to 500x500x800 mm) to suit small-batch R&D or large-scale production.
Power Supply: Three-phase AC power with voltage options (220V/380V/480V) and power ratings from 15 kW to 75 kW, depending on chamber size and temperature requirements.
Control System: Integrated PLC or touchscreen interface with PID temperature control, multi-segment programmable curves, and real-time data logging. Safety features include over-temperature protection, gas flow monitoring, and emergency shutdown.
Material Compatibility: Optimized for sintering SiC ceramics, metal-ceramic composites (e.g., Al-SiC, Cu-SiC), and refractory metals. The furnace structure uses high-purity alumina insulation and ceramic fiber modules for thermal efficiency and longevity.
Applications: Ideal for producing seals, bearings, cutting tools, and aerospace components requiring high wear resistance, thermal stability, and mechanical strength.
Certifications: Complies with international standards (ISO, CE) for safety and performance. Optional upgrades include vacuum pumps, gas purification systems, and post-sintering quenching modules.
This sintering furnace combines robust construction with advanced thermal management, making it a critical tool for industries pushing the boundaries of powder metallurgy and advanced ceramic manufacturing.
(composite metal powders silicon carbide sealing ceramic sintering Powder metallurgy sintering furnace)
Applications of composite metal powders silicon carbide sealing ceramic sintering Powder metallurgy sintering furnace
Composite metal powders, especially those incorporated with silicon carbide (SiC), are changing sophisticated production procedures, especially in the manufacturing of high-performance securing ceramics through powder metallurgy sintering heating systems. These materials are crafted to provide extraordinary mechanical strength, thermal security, and put on resistance, making them perfect for requiring applications across sectors. Silicon carbide, a ceramic recognized for its firmness, corrosion resistance, and ability to stand up to extreme temperature levels, boosts the properties of steel matrices when combined by means of sintering.
In powder metallurgy, sintering furnaces play an important duty in consolidating composite metal-SiC powders into dense, resilient elements. The procedure entails condensing the powder into a wanted form and home heating it below the melting factor to bond particles via diffusion. For securing porcelains– made use of in pumps, shutoffs, and aerospace components– this guarantees leak-proof performance under high-pressure or high-temperature problems. The consistent heating and accurate ambience control in contemporary sintering furnaces prevent oxidation and make certain microstructural homogeneity, critical for parts revealed to harsh or abrasive atmospheres.
Trick applications include aerospace engine seals, where SiC-reinforced compounds resist thermal shock and disintegration from exhaust gases. Automotive sectors use these ceramics in turbocharger seals and brake systems to improve long life and performance. In energy sectors, nuclear and solar thermal plants rely upon sintered SiC seals for activator coolant systems and warmth exchangers as a result of their radiation resistance and thermal conductivity. Industrial equipment benefits from wear-resistant seals in hydraulic systems, minimizing downtime and maintenance costs.
Using composite metal-SiC powders in sintering furnaces additionally supports sustainability by lessening product waste and power usage. Advanced heating systems allow fast cycle times, accurate temperature level gradients, and compatibility with inert or vacuum cleaner environments, guaranteeing high-quality result. Customizable powder blends and sintering specifications better allow customized services for details operational difficulties.
By leveraging the harmony of composite steel powders and silicon carbide in powder metallurgy sintering heaters, manufacturers achieve parts that master performance, longevity, and reliability, satisfying the stringent needs of modern-day engineering applications.
Company Introduction
Welcome to It-Chuiko, a premier international supplier of high-quality silicon carbide powder and silicon carbide ceramics. Our products are renowned for their exceptional hardness, thermal stability, and wear resistance, making them ideal for abrasives, cutting tools, refractory materials, and advanced semiconductor applications. We serve a diverse range of industries, including automotive, aerospace, and electronics, with a commitment to quality and innovation. With state-of-the-art production facilities and rigorous quality control, we ensure that our customers receive superior products tailored to their specific needs. Partner with us for reliable, high-performance materials that drive your business forward.
If you have any questions, please feel free to contact us(nanotrun@yahoo.com).
Payment Methods
T/T, Western Union, Paypal, Credit Card etc.
Shipment Methods
By air, by sea, by express, as customers request.
5 FAQs of composite metal powders silicon carbide sealing ceramic sintering Powder metallurgy sintering furnace
1. What is the primary application of a composite metal powders silicon carbide sealing ceramic sintering furnace?
A sintering furnace designed for composite metal powders and silicon carbide sealing ceramics is primarily used to bond powdered materials into dense, high-strength components through controlled heating. This process is critical in industries like aerospace, automotive, and industrial machinery, where components require exceptional thermal stability, wear resistance, and mechanical strength. It is ideal for producing seals, bearings, and structural parts that operate under extreme conditions.
2. What temperature range and uniformity does this sintering furnace offer?
These furnaces typically operate within a range of 1200°C to 2200°C, depending on the material composition and sintering requirements. Advanced models ensure temperature uniformity within ±5°C across the heating zone, achieved via multi-zone heating elements and precise control systems. This consistency is crucial for preventing defects and ensuring homogeneous densification of silicon carbide or composite metal powders.
3. How does the furnace handle material compatibility for silicon carbide and composite powders?
The furnace is engineered with inert gas or vacuum environments to prevent oxidation during sintering, which is vital for reactive materials like silicon carbide. High-purity alumina or graphite heating elements and insulation materials resist chemical interactions, ensuring compatibility with composite metal powders (e.g., tungsten-carbide blends) and ceramics. Users must pre-process powders to ensure optimal particle size and binder content for successful sintering.
4. What energy efficiency features are incorporated into these sintering furnaces?
Modern designs integrate energy-saving technologies such as advanced insulation (e.g., ceramic fiber modules), recuperative cooling systems, and programmable logic controllers (PLCs) to optimize heating cycles. These features reduce power consumption by up to 30% compared to conventional furnaces. Additionally, rapid cooling mechanisms shorten cycle times, enhancing overall productivity.
5. How durable and low-maintenance is the furnace for industrial-scale operations?
Built with robust materials like refractory metals and ceramics, the furnace resists thermal fatigue and corrosion, ensuring a lifespan of 10+ years with proper maintenance. Routine upkeep involves inspecting heating elements, thermocouples, and seals for wear. Automated self-diagnostic systems alert users to potential issues, minimizing downtime. Minimal residue buildup from silicon carbide or metal powders simplifies cleaning between batches.
(composite metal powders silicon carbide sealing ceramic sintering Powder metallurgy sintering furnace)
REQUEST A QUOTE
RELATED PRODUCTS
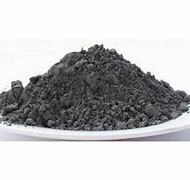
Green silicon carbide abrasive carborundum powder GC glass polishing powder
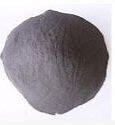
Emery Sand Black Silicon Carbide Carborundum Grit Grain Silicon Carbide Powder Ton
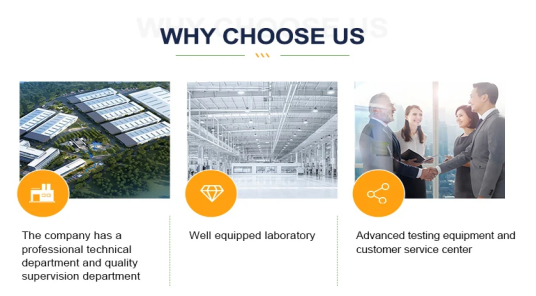
Factory Nano Silicon Carbide Sic powder silicon carbide Raw Material With 99% Purity
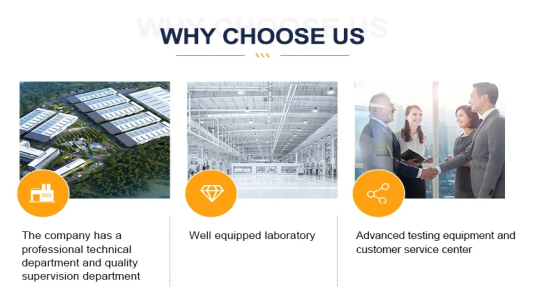
black silicon carbide powder
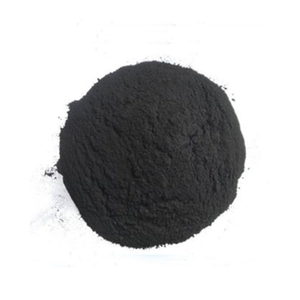
SIC Silicon Carbide Black Silicon Carbide Powder Fine Powder
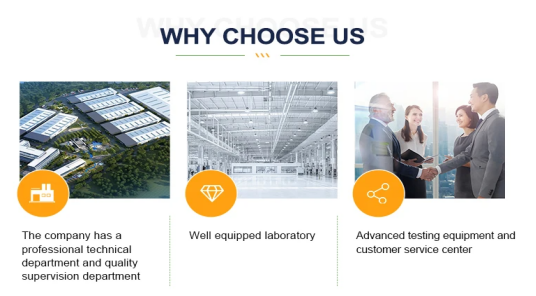