High-Quality Silicon Carbide Products | Advanced Ceramic Solutions
PRODUCT PARAMETERS
Description
Overview of Silicon Carbide Powder
Silicon carbide (SiC) powder is a high-performance ceramic material composed of silicon and carbon. Known for its exceptional hardness, thermal stability, and wear resistance, SiC powder is widely used in abrasives, cutting tools, refractory materials, and advanced technological applications like semiconductors and electric vehicle components.
Features of Silicon Carbide Powder
Exceptional Hardness: One of the hardest known materials, second only to diamond, making it ideal for abrasive and cutting applications.
Thermal Stability: High resistance to thermal shock and can withstand extreme temperatures, enhancing its utility in refractory and high-temperature environments.
Chemical Inertness: Resistant to most chemicals, including acids and alkalis, ensuring durability in harsh conditions.
Wear Resistance: Excellent wear resistance properties make it suitable for demanding mechanical applications.
Electrical Conductivity: Depending on the purity and doping levels, SiC can exhibit varying degrees of electrical conductivity, useful in electronics.
(Black Sic/silicon 10-100mm And Silicon Carbide Powder Sic For Casting)
Specifications of Black Sic/silicon 10-100mm And Silicon Carbide Powder Sic For Casting
Black Silicon Carbide (SiC) 10-100mm and Silicon Carbide Powder (SiC) are high-performance products commonly used in spreading, metallurgy, and refractory applications. Both products are engineered for longevity, thermal resistance, and chemical stability, making certain ideal efficiency popular industrial settings.
** Black Silicon Carbide 10-100mm Requirements **.
This lump-form SiC is produced with carbothermal reduction of high-purity quartz sand and oil coke. It has a minimum of 98% SiC, with trace amounts of totally free carbon (≤ 0.2%) and iron oxide (Fe ₂ O ₃ ≤ 0.5%). The material features a Mohs solidity of 9.5, making it among the hardest industrial abrasives. Its thickness varies in between 3.1-3.2 g/cm ³, and it has a melting point of approximately 2,700 ° C. The 10-100mm dimension range is ideal for use as a recarburizer in iron and steel casting, where it improves carbon content, boosts steel fluidness, and decreases shrinkage defects. Its high thermal conductivity (120-140 W/m · K) makes certain effective warm transfer in furnace cellular linings and refractory applications. The product is also resistant to thermal shock and oxidation, making it suitable for long term usage in high-temperature atmospheres like foundry heating systems.
** Silicon Carbide Powder Specs **.
The SiC powder is offered in great qualities (mesh dimensions from F12 to F220) with pureness degrees surpassing 97%. It has a sharp, angular fragment framework, making certain effective cutting and abrasion homes. Secret chemical elements include SiC (≥ 97%), totally free carbon (≤ 0.3%), and Fe ₂ O ₃ (≤ 0.8%). The powder’s mass thickness is 1.2-1.6 g/cm ³, and it maintains high thermal security up to 1,600 ° C. In spreading, the powder is utilized as an additive in mold and core sands to boost surface area finish and dimensional precision of cast parts. It also acts as a refractory coating to avoid steel infiltration right into molds. When contributed to molten metal, SiC powder acts as a deoxidizer and alloying agent, enhancing solidity and wear resistance in end products.
** Applications **.
Both items are vital in steelmaking, iron casting, and aluminum refining. They minimize power usage by boosting heating system effectiveness and prolonging refractory life-span. Their resistance to thermal expansion and rust ensures consistent performance in aggressive industrial setups. These materials follow worldwide requirements (ASTM, ISO) and are packaged to stop contamination. Suitable for factories, steel plants, and refractory makers, Black SiC swellings and powder supply dependability, cost-effectiveness, and enhanced metallurgical outcomes.
(Black Sic/silicon 10-100mm And Silicon Carbide Powder Sic For Casting)
Applications of Black Sic/silicon 10-100mm And Silicon Carbide Powder Sic For Casting
Black silicon carbide (SiC) is a synthetic ceramic material composed of silicon and carbon, renowned for its phenomenal solidity, thermal conductivity, abrasion resistance, and chemical security. Offered in granular forms (10-100mm) and as fine powder, it is extensively used in casting processes to improve performance, longevity, and effectiveness. In shop applications, 10-100mm Black SiC granules are largely made use of as a refractory material in mold and core production. Their high thermal conductivity makes sure rapid warmth dissipation during metal pouring, minimizing thermal anxiety and lessening flaws like cracks or bending in cast parts. These granules likewise improve mold durability, specifically in high-temperature atmospheres, by withstanding thermal shock and erosion caused by molten metals. This extends mold and mildew lifespan and keeps dimensional precision in complicated spreadings. Furthermore, Black SiC’s chemical inertness protects against responses with molten alloys, protecting metal pureness. Silicon carbide powder, with fragment dimensions ranging from microns to sub-microns, serves as a vital additive in steel spreading. When presented right into molten steels like iron, steel, or aluminum, SiC powder works as a nucleating agent, refining grain frameworks to enhance mechanical properties such as tensile stamina, firmness, and wear resistance. It additionally minimizes shrinking porosity and boosts surface finish by advertising smoother solidification. In sand spreading, SiC powder is combined with molding sands to produce heat-resistant molds with the ability of enduring severe temperatures, guaranteeing consistent casting high quality. Its use in coverings for mold and mildews and cores better protects against steel infiltration and boosts release properties. Industries such as automobile, aerospace, and energy rely on SiC-enhanced castings for components like engine blocks, turbine blades, and pump real estates, where high stamina and thermal tiredness resistance are crucial. Overall, Black SiC granules and powder maximize casting processes by integrating thermal management, mechanical reinforcement, and long life, making them indispensable in modern-day metallurgy.
Company Introduction
Welcome to It-Chuiko, a premier international supplier of high-quality silicon carbide powder and silicon carbide ceramics. Our products are renowned for their exceptional hardness, thermal stability, and wear resistance, making them ideal for abrasives, cutting tools, refractory materials, and advanced semiconductor applications. We serve a diverse range of industries, including automotive, aerospace, and electronics, with a commitment to quality and innovation. With state-of-the-art production facilities and rigorous quality control, we ensure that our customers receive superior products tailored to their specific needs. Partner with us for reliable, high-performance materials that drive your business forward.
If you have any questions, please feel free to contact us(nanotrun@yahoo.com).
Payment Methods
T/T, Western Union, Paypal, Credit Card etc.
Shipment Methods
By air, by sea, by express, as customers request.
5 FAQs of Black Sic/silicon 10-100mm And Silicon Carbide Powder Sic For Casting
What is Black Silicon Carbide (SiC) 10-100mm and Silicon Carbide Powder used for in casting?
Black Silicon Carbide (SiC) 10-100mm grains and powder are abrasive, refractory materials used in metal casting for mold and core production. The granular form (10-100mm) strengthens molds, improves heat resistance, and reduces thermal expansion. The powder is blended into coatings or refractory mixes to enhance surface finish, prevent metal penetration, and improve mold durability under high temperatures.
Why choose Silicon Carbide over other refractory materials for casting?
Silicon Carbide offers superior thermal conductivity, high hardness, and exceptional thermal shock resistance. It maintains structural stability at temperatures up to 1600°C, outperforming quartz or clay-based materials. Its low thermal expansion minimizes cracking, while its abrasion resistance extends mold lifespan, reducing replacement costs and downtime in foundries.
What sizes of Black SiC are ideal for different casting applications?
The 10-30mm grains are used for bulk mold reinforcement in large castings like steel ingots. Medium sizes (30-60mm) suit general-purpose molds for iron or aluminum. Larger grains (60-100mm) provide extra thermal buffering in high-mass pours. The powder (micron to sub-millimeter grades) is ideal for creating smooth mold coatings or mixing into refractory linings for precision castings.
How is Silicon Carbide Powder applied in casting processes?
The powder is mixed with binders or solvents to create slurry coatings applied to mold surfaces. This layer prevents molten metal from sticking, reduces gas defects, and improves surface finish. It’s also added to sand molds or ceramic cores to boost refractoriness. For ferrous metals, SiC powder helps control cooling rates, minimizing shrinkage flaws.
Are there safety or storage guidelines for handling SiC products?
Store Black SiC grains and powder in dry, sealed containers to prevent moisture absorption, which can affect performance. Use gloves and masks when handling the powder to avoid inhalation or skin irritation. While chemically inert, avoid mixing with strong acids or alkalis. The material is non-combustible and has no shelf-life limitations if stored properly.
(Black Sic/silicon 10-100mm And Silicon Carbide Powder Sic For Casting)
REQUEST A QUOTE
RELATED PRODUCTS
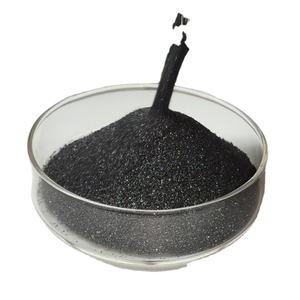
Factory 500nm CAS 409-21-2 99% Alpha/Beta Silicon Carbide Powder SiC Powder
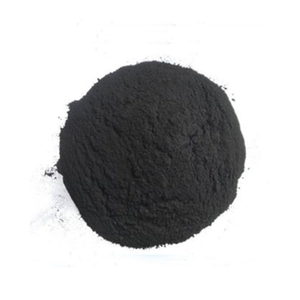
SIC Silicon Carbide Black Silicon Carbide Powder Fine Powder
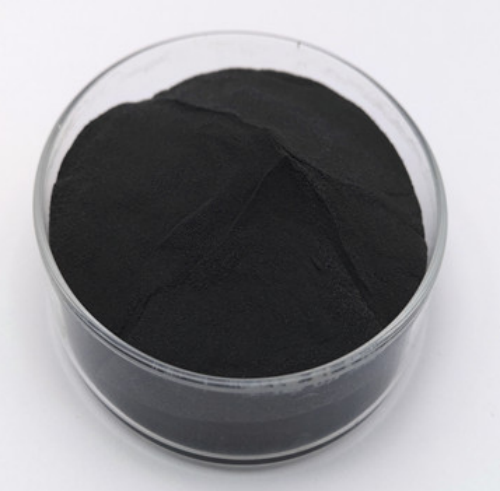
Factory Supply Black Silicon Carbide Powder Particle Size Green Silicon Carbide For Furnace
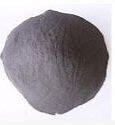
Emery Sand Black Silicon Carbide Carborundum Grit Grain Silicon Carbide Powder Ton
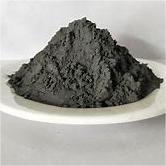
composite metal powders silicon carbide sealing ceramic sintering Powder metallurgy sintering furnace
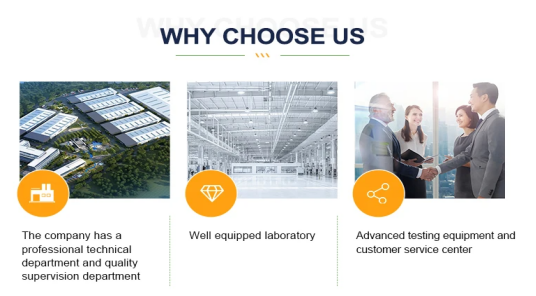