High-Quality Silicon Carbide Products | Advanced Ceramic Solutions
PRODUCT PARAMETERS
Description
Overview of Silicon Carbide Ceramic
Silicon carbide (SiC) ceramic is a high-performance material known for its exceptional hardness, wear resistance, and thermal stability. It is widely used in cutting tools, abrasives, automotive components, and high-temperature applications due to its superior mechanical properties and chemical inertness.
Features of Silicon Carbide Ceramic
High Hardness: SiC ceramics are among the hardest known materials, making them ideal for abrasive and cutting applications.
Thermal Stability: They can withstand extreme temperatures without degrading, making them suitable for high-temperature environments.
Wear Resistance: Exceptional resistance to wear and abrasion ensures long-lasting performance.
Chemical Inertness: Resistant to most chemicals, including acids and alkalis, enhancing their durability in harsh conditions.
Low Thermal Expansion: Minimal expansion or contraction with temperature changes, ensuring dimensional stability.
Electrical Conductivity: Some forms of SiC ceramics exhibit semiconducting properties, useful in electronic devices.
(Sintering Of Silicon Carbide Ceramics With Additives Industrial Furnace)
Specifications of Sintering Of Silicon Carbide Ceramics With Additives Industrial Furnace
The sintering of silicon carbide (SiC) ceramics with additives in an industrial furnace requires precise temperature control, advanced atmosphere management, and robust material handling capabilities. Designed for high-performance applications, these furnaces operate at temperatures up to 2200°C, accommodating the sintering needs of SiC-based composites enhanced with additives such as boron, aluminum, or carbon. The furnace chamber is constructed from high-purity graphite or refractory metals to withstand extreme thermal and chemical conditions, ensuring minimal contamination during the process.
Atmosphere control is critical, with options for inert gas environments (argon, nitrogen) or vacuum settings (up to 10⁻³ mbar) to prevent oxidation and promote densification. Gas flow systems are adjustable to maintain uniform pressure and composition, tailored to specific additive interactions. Heating elements, typically graphite or molybdenum disilicide (MoSi₂), enable rapid heating rates (5–20°C/min) and precise temperature uniformity (±5°C across the chamber). Cooling systems incorporate forced gas quenching or controlled slow cooling to optimize microstructure development and minimize residual stresses.
The furnace features modular chamber designs, with customizable sizes (e.g., 200x200x200 mm to 1000x1000x2000 mm) to accommodate batch or continuous production. Advanced insulation using ceramic fiber or carbon-carbon composites ensures energy efficiency, reducing operational costs. Real-time monitoring via integrated thermocouples, pyrometers, and gas analyzers allows for automated process adjustments through programmable logic controllers (PLCs). Data logging and remote access capabilities support quality control and compliance with industry standards (ISO, ASTM).
Safety mechanisms include over-temperature shutdowns, pressure relief valves, and emergency cooling protocols. The furnace is compatible with debinded SiC green bodies, enabling net-shape sintering with minimal post-processing. Applications span aerospace (turbine components), automotive (brake discs), energy (semiconductor substrates), and industrial wear-resistant parts. Optional configurations include multi-zone heating for graded materials and hybrid sintering (pressure-assisted or microwave-enhanced). Maintenance is streamlined via accessible heating elements and replaceable insulation modules, ensuring long-term reliability.
This industrial furnace is engineered for scalability, supporting R&D prototyping to mass production, with a focus on repeatability, energy efficiency, and compatibility with advanced SiC ceramic formulations. Technical support includes process optimization and after-sales service to adapt to evolving material science requirements.
(Sintering Of Silicon Carbide Ceramics With Additives Industrial Furnace)
Applications of Sintering Of Silicon Carbide Ceramics With Additives Industrial Furnace
Sintering silicon carbide (SiC) ceramics with additives is a critical process in manufacturing advanced materials for high-performance industrial furnace applications. Silicon carbide’s exceptional thermal stability, mechanical strength, and resistance to wear, corrosion, and thermal shock make it ideal for extreme environments. The addition of sintering aids like boron, aluminum, or carbon enhances densification during the sintering process, improving structural integrity and enabling tailored properties for specific industrial needs.
In metallurgical furnaces, sintered SiC ceramics with additives are used for components like radiant tubes, burners, and kiln furniture. These parts endure temperatures exceeding 1,500°C while maintaining dimensional stability, ensuring efficient heat transfer and prolonged service life in metal heat treatment, sintering, or melting processes. The material’s low thermal expansion minimizes cracking under rapid temperature changes.
For semiconductor manufacturing, SiC ceramics sintered with additives serve as susceptors, wafer boats, and diffusion plates in epitaxial growth and CVD furnaces. Their purity and resistance to chemical erosion ensure contamination-free processing of silicon wafers, while high thermal conductivity enables uniform temperature distribution critical for producing high-quality semiconductors.
In the energy sector, SiC-based heating elements and insulation components are integral to electric furnaces used in glass manufacturing and ceramic production. Additives improve electrical conductivity, allowing SiC to function as energy-efficient heating elements that operate at ultra-high temperatures with minimal degradation.
Chemical processing furnaces leverage SiC’s corrosion resistance by using sintered components like liners, nozzles, and thermocouple sheaths in aggressive environments involving acids, alkalis, or molten salts. Additives enhance density, reducing porosity to prevent penetration by corrosive agents.
Environmental applications include SiC ceramic filters and catalyst supports in industrial waste incineration furnaces. Their thermal resilience ensures efficient particulate filtration and catalytic conversion of harmful emissions at high temperatures.
The use of additives in sintering SiC ceramics optimizes mechanical, thermal, and electrical properties, making them indispensable in industrial furnaces that demand reliability, efficiency, and longevity. By enabling precise control over microstructure and performance, sintered SiC ceramics support advancements in high-temperature industrial processes across sectors like metallurgy, electronics, energy, and environmental engineering.
Company Introduction
Welcome to It-Chuiko, a premier international supplier of high-quality silicon carbide powder and silicon carbide ceramics. Our products are renowned for their exceptional hardness, thermal stability, and wear resistance, making them ideal for abrasives, cutting tools, refractory materials, and advanced semiconductor applications. We serve a diverse range of industries, including automotive, aerospace, and electronics, with a commitment to quality and innovation. With state-of-the-art production facilities and rigorous quality control, we ensure that our customers receive superior products tailored to their specific needs. Partner with us for reliable, high-performance materials that drive your business forward.
If you have any questions, please feel free to contact us(nanotrun@yahoo.com).
Payment Methods
T/T, Western Union, Paypal, Credit Card etc.
Shipment Methods
By air, by sea, by express, as customers request.
5 FAQs of Sintering Of Silicon Carbide Ceramics With Additives Industrial Furnace
**What is the role of additives in sintering silicon carbide ceramics?**
Additives such as boron, carbon, or aluminum oxide are used to enhance the sintering process by lowering the required temperature and promoting densification. They act as sintering aids, reducing porosity and improving mechanical properties. Additives like boron form liquid phases that facilitate particle rearrangement, while carbon suppresses surface oxidation, ensuring a cleaner, stronger final product.
**What temperature and atmosphere are required for sintering silicon carbide with additives?**
Sintering typically occurs between 1800°C and 2200°C in an inert atmosphere (argon or nitrogen) or vacuum. Additives allow lower temperatures compared to pure silicon carbide sintering. The atmosphere prevents oxidation and ensures chemical stability. Precise control of temperature gradients and gas flow is critical to achieving uniform density and minimizing defects.
**Which industrial furnaces are suitable for sintering silicon carbide ceramics with additives?**
High-temperature electric resistance furnaces, such as vacuum sintering furnaces, gas-pressure sintering furnaces, or hot isostatic pressing (HIP) furnaces, are commonly used. These furnaces provide precise temperature control, uniform heating, and adjustable atmospheres. Continuous or batch furnaces may be selected based on production scale and specific additive requirements.
**What are the key challenges in sintering silicon carbide with additives?**
Challenges include maintaining additive homogeneity to prevent uneven densification, managing thermal stresses to avoid cracking, and controlling atmospheric conditions to suppress oxidation. Additive volatility at high temperatures can also complicate process stability. Advanced furnace design and real-time monitoring systems help mitigate these issues.
**What benefits do additives provide in sintered silicon carbide ceramics?**
Additives improve sinterability, enabling lower energy consumption and reduced production costs. They enhance final product properties, including higher density, superior fracture toughness, and better thermal shock resistance. This makes the ceramics suitable for demanding applications like aerospace components, semiconductor manufacturing tools, and high-temperature industrial wear parts.
(Sintering Of Silicon Carbide Ceramics With Additives Industrial Furnace)
REQUEST A QUOTE
RELATED PRODUCTS
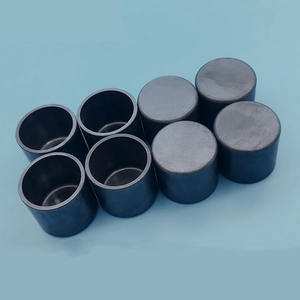
High Quality Silicon Carbide Factory Black Silicon Carbide With Good

Boron carbide Insert Silicon carbide Tiles From China
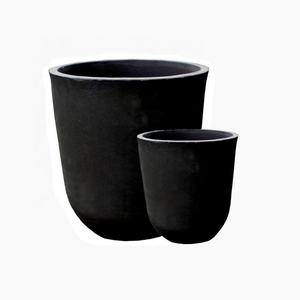
RBSIC SISIC SIC silicon carbide sic ceramics refractory cut plate

High quality hexagon sic silicon carbide ceramic plate for refractory industry
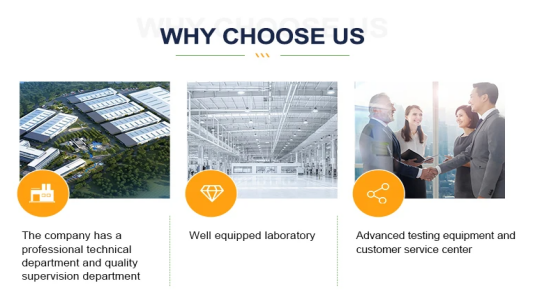
High temperature silicon carbide ceramic plates 1650C refractory silicon carbide tiles for kiln shelf
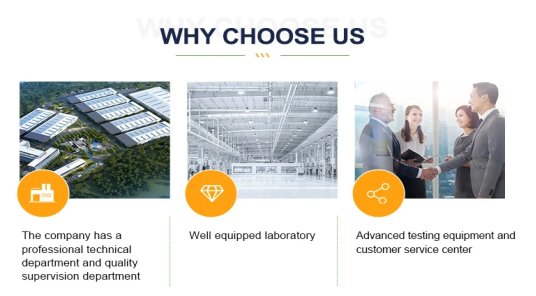